India’s steel ministry is eyeing collaborations with Japan to reduce carbon emissions in steel-making. It is also considering introducing mechanisms for implementing specific technologies “through project funding from Japanese institutions”, an internal note of the ministry, accessed by businessline, shows.
One of the two decarbonisation projects currently underway include use of green hydrogen as an alternative fuel to partly replace coal; the second includes developing new coke-making technologies that use less coking coal and show higher oven productivity.
India’s carbon emissions in the steel-making sector is among the highest worldwide, primarily because it uses raw materials like iron ore and coal instead of scrap or other alternatives.
Also read
“Mechanism for implementing these technologies in India through project funding from Japanese institutions (is being considered),” the note mentions.
Ministry documents show the steel-making process in India emits carbon dioxide of 2.2-2.7 tonnes per tonne of crude steel produced (T/TCS), as against a global average of 1.8-2 T/TCS. Emissions have dipped slightly in FY23, over the previous fiscal.
India is the second largest crude steel producer globally at 161 million tonnes (mt) of installed capacity and production of 122 mt.
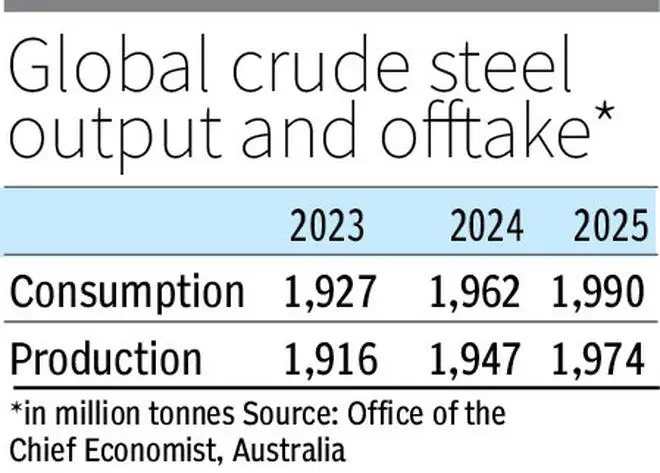
Use of green hydrogen
The ministry’s internal note mentions that ‘COURSE 50’ — one of the two projects under consideration — aims to reduce carbon dioxide emissions from blast furnaces by 30 per cent through “part replacement of coke with hydrogen”. The COURSE 50 project was earlier introduced across Japanese steel mills in a bid to reduce carbon emissions.
Technologies such as injection of reformed coke oven gas (COG) and carbon-capture-and-use-and-storage (CCUS) aim to lower the emission intensity of blast furnaces.
The World Steel Association, in a recent study, mentioned that CCUS technologies “can be retro-fitted” into existing systems to cut carbon emissions, which are projected to touch 8 billion tonnes by 2050.
Incidentally, Japanese steel major Nippon Steel Corporation had said in August 2023 that it has been working on ‘Super COURSE 50’, a technique to reduce carbon dioxide emissions by using heated hydrogen, at the East Nippon Works Kimitsu Area since May 2022. It reported 22 per cent reduction in carbon dioxide emission from the blast furnace, and targets 30-plus per cent reduction by 2023.
India aims to cut carbon emissions by 45 per cent by 2030, 70 per cent by 2047, and 100 per cent by 2070.
Plans are afoot to introduce l,500 GW of non-fossil fuel energy by 2030, with priority accorded to replacing thermal power usage with renewable energy in the steel industry, the note reads.
Additionally, under the National Green Hydrogen Mission the country aims to generate 5 million tonnes of green hydrogen .
Coke making
The second project, called SCOPE 21, is a high-end coke making process developed under a national project by the Japanese steel industry. It enables use of large amounts of non-coking coal or slightly coking coal for coke production to attain higher plant productivity.
Nippon Steel, in a review paper published earlier, said the SCOPE 21 process involves a fluidised bed coal dryer, a pneumatic preheater for rapid heating of coal to 330–380 degrees C, and a hot briquetting machine for coal fines. Commercial plants using the process were built at Oita and Nagoya Works in 2008 and 2013, respectively, and have been in steady operation since. The process enables the use of a markedly larger amount of non- or slightly-coking coal for coke production, compared to the conventional process, and attains far higher plant productivity.
In India, steel techno-economic parameters are yet to catch up with global best practices.
For instance, blast furnace productivity in India is 1.8-3.5 tonnes per cubic metres per day, against the global parameter of 2.5-3.5 tonnes per cubic metres per day.
Similarly, in the blast furnace route the coke usage (called BF Coke Rate) in India is a high 337-457 kg/ tonne of hot metal produced; against a global best practice of 300-350 kg / tonne of hot metal produce.
Comments
Comments have to be in English, and in full sentences. They cannot be abusive or personal. Please abide by our community guidelines for posting your comments.
We have migrated to a new commenting platform. If you are already a registered user of TheHindu Businessline and logged in, you may continue to engage with our articles. If you do not have an account please register and login to post comments. Users can access their older comments by logging into their accounts on Vuukle.